Graphite electrodes are the unsung heroes inside intense electric arc furnaces (EAFs) and ladle furnaces (LFs). They carry massive amounts of electrical current to melt scrap metal or refine steel. However, these crucial components don’t last forever. Understanding why graphite electrodes need regular replacement is key to maintaining efficient furnace operation, ensuring product quality, and managing operational costs effectively. This article dives deep into the reasons behind electrode consumption, the factors influencing it, and why timely replacement is not just a maintenance task, but a strategic necessity for anyone operating arc furnaces, especially for professionals like Mark Thompson in the USA who rely on sourcing high-quality graphite products for steel mills and foundries. Discover how managing your graphite electrode lifecycle impacts your bottom line.
1. What Exactly is a Graphite Electrode and Its Role in a Furnace?
A graphite electrode is essentially a large, cylindrical rod made primarily from high-purity petroleum coke, needle coke, and coal tar pitch binder. These materials are mixed, shaped, baked, impregnated, baked again, and finally graphitized at extremely high temperatures (around 3000°C). This process gives the electrode its unique and vital properties: excellent electrical conductivity, high thermal shock resistance, and the ability to withstand the intense heat inside an electric arc furnace. Their primary function is to act as a conductive pathway, carrying enormous electrical energy from the power source down into the furnace.
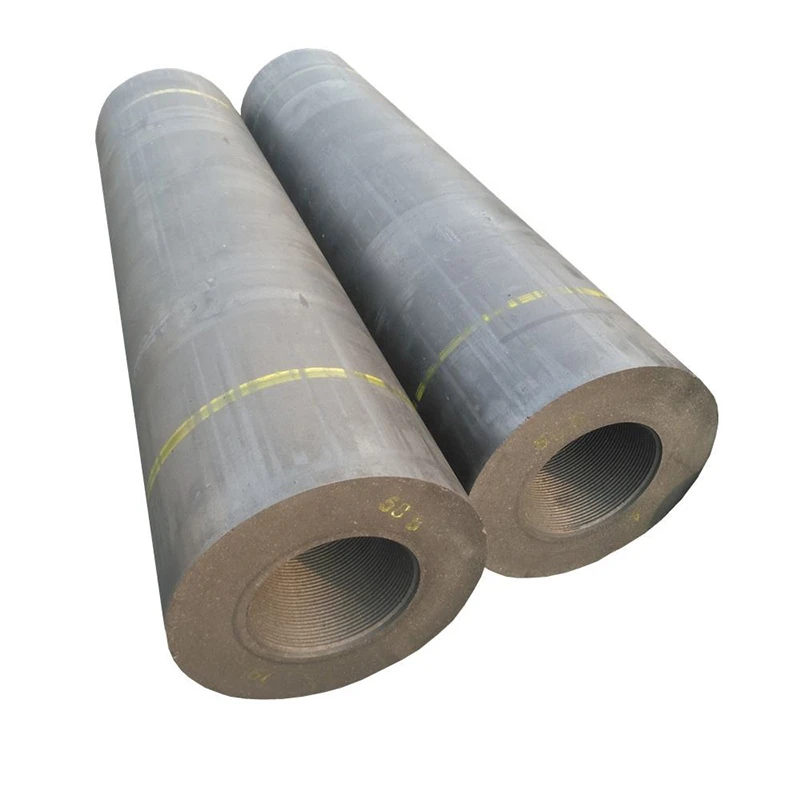
Inside the furnace, the tip of the electrode creates a powerful electric arc with the metallic charge (scrap steel or other metal) or the molten metal bath. This electric arc generates incredible heat – often exceeding 3,000°C (5,400°F) – which is necessary to melt the solid charge or smelt and refine the liquid metal. Think of it like a giant, super-powered welding rod designed for melting tons of metal. Without these electrodes and graphite components, the electric arc furnace simply couldn’t operate or reach the temperature required for steelmaking and other metallurgical processes. They are fundamental to the operation.
The choice of graphite as the material is deliberate. Graphite maintains its strength at very high temperatures, conducts electricity efficiently (low resistance), and handles rapid temperature changes (thermal shock) without easily breaking. Different grades exist, like Regular Power (RP), High Power (HP), and Ultra-High Power (UHP), tailored to the specific demands and power levels of different furnace types. An Ultra-high power graphite electrode is designed for the most demanding arc furnaces, offering lower electrical resistance and higher current-carrying capacity to maximize melting efficiency.
2. The Inevitable Reality: Why Does Graphite Electrode Consumption Occur?
Despite their robustness, graphite electrodes are consumable items. They must be replaced periodically because they gradually get shorter and thinner during furnace operation. This consumption is an unavoidable consequence of the harsh environment they operate in. The intense heat of the electric arc, the chemical reactions with gases and slag inside the furnace, and physical stresses all contribute to the gradual wearing away of the graphite material. It’s not a matter of if an electrode will be consumed, but when and how quickly.
Understanding that consumption is inherent is crucial for planning and budgeting. Trying to extend the life of an electrode beyond its optimal point can actually increase overall costs through reduced efficiency, potential damage to equipment, and lower quality metal production. The loss of graphite happens mainly through two mechanisms: tip consumption (sublimation and reaction at the arc) and sidewall consumption (oxidation). We’ll explore these in more detail next.
The key takeaway is that graphite electrode consumption is a normal part of the electric arc furnace process. Factors like the quality of the electrode itself, the furnace operating parameters (voltage, current), the type of steel being produced, and the skill of the operators all play a role in how fast an electrode is used up. Therefore, planning for regular replacement is essential for continuous and efficient operation.
3. How Do Electrodes Wear Out? Breaking Down Electrode Loss Mechanisms.
Graphite electrode consumption isn’t a single process but rather a combination of factors working together in the aggressive furnace environment. Understanding these mechanisms helps in identifying ways to potentially reduce the rate of loss.
-
Tip Consumption (Sublimation & Reaction): The very tip of the electrode, where the electric arc forms, experiences the most extreme conditions.
- Sublimation: At the arc’s incredibly high temperatures (reaching over 3000°C), the solid graphite doesn’t melt; it turns directly into gas (sublimates). This continuous vaporization slowly eats away at the electrode tip length.
- Chemical Reaction: The intense heat also promotes chemical reactions between the carbon in the graphite and components in the slag or molten metal bath. This forms gases like carbon monoxide, further consuming the electrode tip.
-
Sidewall Consumption (Oxidation): The sides of the electrode column extending above the molten bath are exposed to the hot furnace atmosphere, which contains oxygen (from air ingress or process reactions).
- Oxidation: At high temperatures, the carbon in the graphite readily reacts with oxygen to form carbon dioxide (CO2) and carbon monoxide (CO) gases. This "burns" away the graphite from the sides, reducing the electrode‘s diameter. This is often the largest component of electrode consumption, sometimes accounting for over 50% of the total loss. The rate of oxidation tends to increase significantly with higher temperature and greater oxygen availability.
-
Breakage and Spalling: While less continuous than tip and sidewall consumption, physical damage can cause significant and sudden electrode loss.
- Thermal Shock: Rapid heating or cooling cycles, especially when power is switched on/off abruptly or when cooler scrap metal comes into contact with a hot electrode, can cause thermal stress, leading to cracks or pieces breaking off (spalling). High thermal shock resistance is a key quality feature.
- Mechanical Stress: Rough handling during installation or replacement, scrap cave-ins within the furnace hitting the electrode, or excessive vibration can lead to breakage. Sometimes, incorrect jointing (connecting a new electrode section) can create weak points.
- Surface Cracks: Small surface cracks, potentially originating from manufacturing or handling, can propagate under stress and heat, eventually causing a larger fracture or crack.
Managing electrode consumption involves addressing all these factors, from using high-quality electrodes with good shock resistance to optimizing furnace practices and ensuring careful handling and installation.
4. What Key Factors Influence the Rate of Electrode Consumption?
The rate at which a graphite electrode is consumed isn’t fixed; it varies significantly based on several interconnected factors. Understanding these can help operators and procurement managers like Mark make informed decisions.
-
Electrode Quality: This is paramount.
- Material Purity & Structure: Electrodes made from high-quality needle coke with a uniform structure generally have lower electrical resistance and better thermal shock resistance, leading to lower consumption. Impurities can increase resistance and susceptibility to oxidation. This is why sourcing from a reputable Professional Graphite Electrode Factory adhering to international standards is crucial.
- Density: Higher density usually means better resistance to oxidation.
- Machining Precision: Poorly machined threads on the electrode and connecting nipple can lead to loose joints, higher electrical resistance at the contact point, overheating, and potential breakage.
-
Furnace Operating Parameters: How the furnace is run directly impacts electrode life.
- Current Density & Voltage: Higher electrical loads (especially excessive current density) increase tip sublimation and overall temperature, accelerating consumption. Operating at the optimal voltage and current profile for the specific phase of the melt is key.
- Arc Length & Stability: A stable, appropriately long electric arc is more efficient and less damaging than a wildly fluctuating or excessively short arc, which can increase heat transfer to the sidewalls and increase consumption.
- Oxygen Usage: Practices like oxygen lancing (injecting oxygen to speed up melting or refining) significantly increase the oxidative environment, accelerating sidewall consumption. Careful control is needed.
- Power-On Time: Simply put, the longer the furnace is operating under power, the more time the electrode spends being consumed. Efficient tap-to-tap times (the total cycle time for one batch of steel) help reduce overall consumption per ton of steel.
-
Furnace Conditions & Environment:
- Scrap Quality & Charging: Very light or poorly distributed scrap can lead to arc instability and flare-ups hitting the electrode sides. Heavy scrap falling unexpectedly can cause mechanical breakage.
- Slag Practice: The composition and foaming of the slag layer covering the molten metal can affect heat radiation to the electrode sidewalls. A good foaming slag can shield the electrode and reduce oxidation and heat loss.
- Fume Extraction System: An efficient fume system helps control the furnace atmosphere but can also draw in more air ( oxygen), potentially increasing oxidation if not balanced correctly.
- Water Leaks: Water leaking into the furnace (e.g., from cooling panels) can react violently and also increase the oxidizing potential of the atmosphere, harming the electrode.
By carefully considering these factors, steelmakers can work towards optimizing their processes to reduce unnecessary electrode consumption and lower operating costs. This often involves a combination of using the right quality electrode for the job and fine-tuning furnace practices.
5. Can Operational Practices Significantly Affect Electrode Loss?
Absolutely. While electrode quality sets a baseline for potential performance, the day-to-day operational practices within the steel plant or foundry have a massive impact on actual graphite electrode consumption and the frequency of replacement. Seemingly small details in how the furnace is operated and how electrodes are handled can add up to significant differences in electrode life and overall efficiency. Poor practices can easily negate the benefits of using a premium electrode, leading to higher costs and potential production disruptions.
Consider the assembly and installation process. Joining electrode sections requires precision and care.
- Cleanliness: Ensure that the electrode sockets and nipple threads are perfectly clean before joining. Dirt or debris can prevent proper contact, leading to high resistance and overheating at the joint, potentially causing it to loosen, crack, or fail during operation.
- Torque: Applying the correct tightening torque using a calibrated torque wrench is critical. Under-tightening leads to poor electrical contact and overheating. Over-tightening can stress the graphite and cause the socket or nipple thread to crack or strip, leading to joint failure. Following the manufacturer’s specifications is a strict requirement.
- Alignment: Ensuring the upper and lower electrode sections are perfectly aligned during assembly prevents undue stress on the joint during operation.
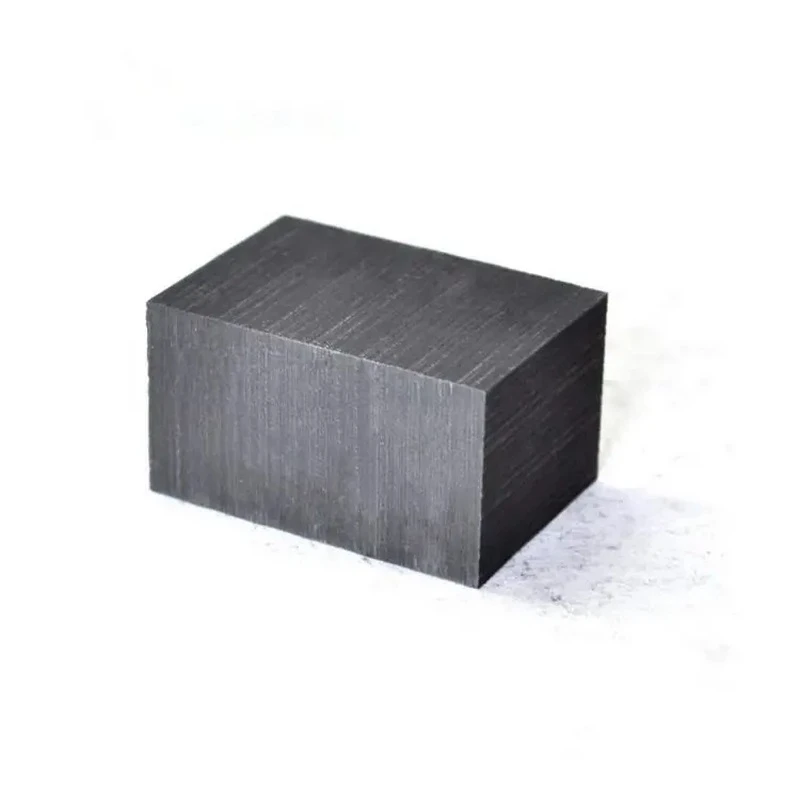
During the melting process itself, operator actions are key:
- Arc Regulation: Skilled operators use the furnace controls to maintain a stable electric arc, adjusting electrode position, voltage, and current appropriately throughout the melt cycle. Avoiding excessively long arcs (which radiate more heat to sidewalls) or short arcs (which can cause current surges) helps minimize consumption.
- Scrap Charging: Careful loading of scrap metal to avoid heavy impacts on the electrodes prevents mechanical breakage. A well-distributed charge promotes stable melting.
- Foamy Slag Practice: Maintaining a good, deep layer of foamy slag shields the electrodes from arc radiation and oxygen, significantly reducing both tip and sidewall consumption. This requires careful control of slag-making additions.
- Power Programs: Utilizing optimized power profiles that match the stage of melting (e.g., boring, melting, refining) ensures efficient energy use and avoids unnecessary stress on the electrodes. Rapid power changes should be minimized to reduce thermal shock.
- Maintenance: Regular maintenance of electrode holders, clamps, and the positioning system ensures good electrical contact and precise control, reducing energy consumption and preventing problems. Water leaks must be addressed promptly.
These examples illustrate that careful operation and maintenance are not optional extras but essential practices to control electrode consumption. Investing in operator training and adhering to best practices can significantly reduce the amount of time an electrode lasts and lower the overall cost per ton of steel produced.
6. Why is Regular Replacement More Than Just Maintenance? The Efficiency Factor.
Thinking of graphite electrode replacement solely as a routine maintenance task misses the bigger picture. Timely and proper replacement is fundamentally linked to the overall efficiency, productivity, and profitability of the electric arc furnace operation. Delaying replacement or using an electrode past its optimal lifespan might seem like saving money in the short term, but it often leads to greater costs and inefficiencies down the line. Regular replacement is a strategic decision that impacts multiple aspects of production.
Firstly, efficiency hinges on the electrode‘s ability to conduct electricity with minimal loss. As an electrode wears down, its diameter decreases, and its tip shape may become suboptimal. A thinner electrode has higher electrical resistance, meaning more energy is lost as heat within the electrode itself rather than being delivered effectively to the melt. This increase in resistance can force the furnace to draw more power to achieve the same melting rate, leading to higher energy consumption per ton of steel. Replacing the electrode ensures that the electrical circuit remains efficient.
Secondly, electrode condition directly affects arc stability and heat transfer. A worn or damaged electrode tip can lead to an unstable or deflected electric arc. This reduces the efficiency of heat transfer to the metal bath and can increase heat loss to the furnace walls and roof, potentially damaging refractories. An unstable arc also makes process control more difficult. Installing a new electrode section restores the optimal geometry for a stable, focused arc, ensuring efficient melting and refining.
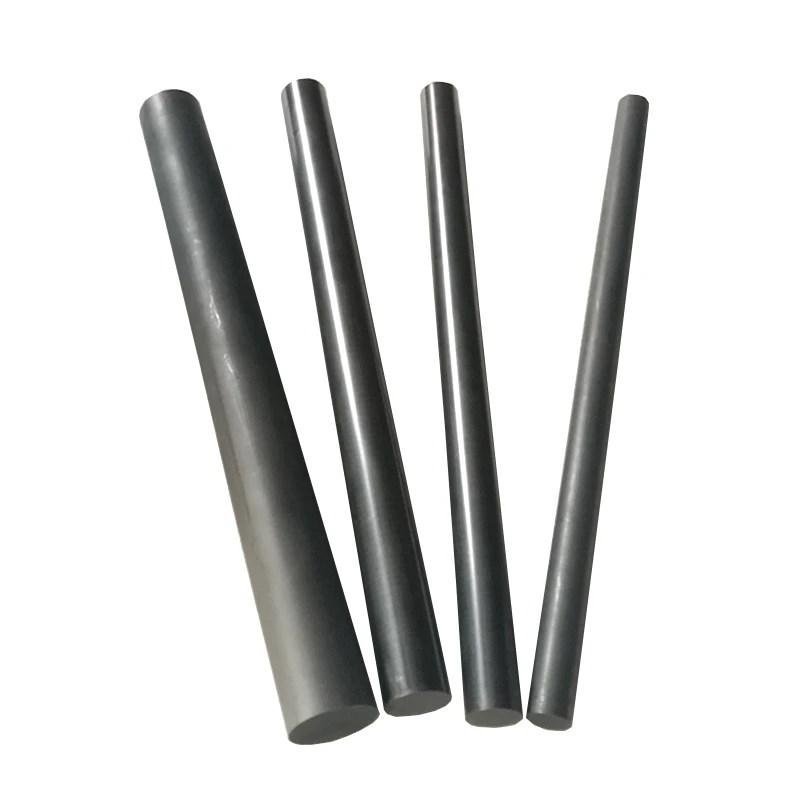
Thirdly, delaying replacement increases the risk of electrode breakage. A severely worn or cracked electrode is much more likely to fail catastrophically during operation. An electrode break can cause significant downtime for removing electrodes fragments from the furnace, potential damage to the furnace itself, contamination of the steel bath with large pieces of carbon, and safety hazards. The cost of lost production and potential repairs far outweighs the cost of a timely replacement. Regular replacement based on condition monitoring and planned schedules helps prevent these costly incidents. Therefore, establishing a clear replacement factor based on wear and operational data is key to maintain consistent production.
7. What are the Telltale Signs That a Graphite Electrode Needs to Be Replaced?
Operators and maintenance crews need to be vigilant in monitoring the condition of graphite electrodes to determine the right time for replacement. While scheduled replacement based on average consumption rates is common, visual inspection and monitoring operational parameters can reveal signs that an electrode section must be replaced sooner to maintain efficiency and prevent failure. Waiting for an electrode to break is never the optimal strategy.
Here are some key indicators:
- Excessive Tip Consumption / "Penciling": While tip consumption is normal, if an electrode tip starts to wear down into a very sharp, pointed shape (like a pencil), it indicates potentially unstable arc conditions or overly aggressive operation. This shape can lead to poor current distribution and increased risk of breakage. It might signal a need to review operating practices or replace the section.
- Significant Reduction in Diameter: Noticeable thinning of the electrode column due to sidewall oxidation reduces its current-carrying capacity and mechanical strength. Standards often define a minimum safe operating diameter. Once an electrode section approaches this limit, replacement is necessary. Monitoring the diameter over time helps predict the replacement point.
- Visible Cracks: Any visible cracks, whether longitudinal (along the length) or transverse (across the diameter), are serious warning signs. Cracks can propagate rapidly under thermal and mechanical stress, leading to sudden failure. Even small cracks warrant close monitoring, and significant ones necessitate immediate replacement. Thermal shock is a common culprit.
- Spalling or Surface Damage: Chunks of graphite missing from the surface (spalling) indicate thermal stress or potential internal inconsistencies. Deep gouges from scrap impacts can also create stress concentration points. Significant surface damage weakens the electrode and requires replacement.
- Overheating at Joints: Discoloration or glowing at the joint between electrode sections indicates high electrical resistance at the contact point. This could be due to improper cleaning during installation, incorrect tightening torque, or damaged threads. An overheating joint is inefficient and risks failure; the connection needs to be checked, and potentially the sections involved may need replacement.
- Operational Data Trends: Monitoring trends like increasing electrical resistance, unstable arc behavior (requiring frequent operator intervention), or unexplained increases in energy consumption can indirectly point towards electrode issues requiring investigation and potential replacement.
- Reaching Predefined Length: In many operations, electrodes are used until they reach a predetermined minimum stub length. This is often dictated by the mechanical limits of the electrode holder or to ensure sufficient length remains for safe handling during replacement.
Regular inspections, both visual and potentially using measurement tools, combined with monitoring furnace performance data, are essential to identify these signs promptly and ensure that the electrode replacement happens before problems arise.
8. How Often is Graphite Electrode Replacement Typically Required?
The frequency of graphite electrode replacement – specifically, adding a new electrode section to the top of the column as the bottom consumes – varies widely depending on the factors we’ve discussed: furnace type and size, operating practices, electrode quality, and the type of steel being produced. There isn’t a single "one-size-fits-all" answer, but we can talk about typical ranges and the concept of electrode consumption rate.
Electrode consumption is usually measured in kilograms (kg) or pounds (lbs) of graphite consumed per metric ton (or short ton) of liquid steel produced (kg/t or lbs/t). Typical consumption rates can range from:
- Modern AC Electric Arc Furnaces (EAFs) using UHP electrodes: 0.8 to 2.5 kg/t (1.6 to 5 lbs/t)
- DC Electric Arc Furnaces (often lower consumption): 0.6 to 1.8 kg/t (1.2 to 3.6 lbs/t)
- Ladle Furnaces (LFs) (lower power, refining focus): 0.2 to 0.8 kg/t (0.4 to 1.6 lbs/t)
- Older or less optimized furnaces, or those melting difficult scrap: Rates can be significantly higher.
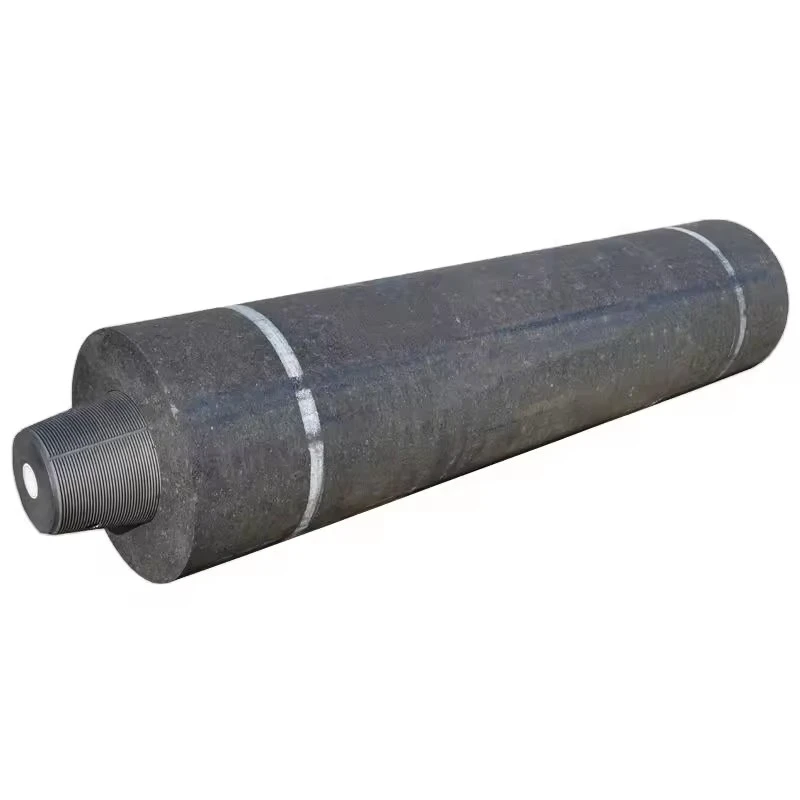
So, how does this translate to replacement frequency? Let’s consider an example:
A large UHP electrode might be 600mm (24 inches) in diameter and 2700mm (106 inches) long, weighing around 1600 kg. If a furnace produces 100 tons of steel per heat (batch) and has an electrode consumption rate of 1.5 kg/t, it consumes 150 kg of graphite per heat (100 t 1.5 kg/t).
To consume the entire usable weight of one electrode section (let’s estimate 1500 kg usable weight), it would take approximately 10 heats (1500 kg / 150 kg/heat). If the furnace completes a heat every hour (tap-to-tap time), a new electrode section would need to be added roughly every 10 operating hours per phase*. Since EAFs typically have three electrode columns (phases), a replacement (adding a new section to one of the columns) might occur roughly every 3-4 hours of operation somewhere on the furnace.
This is a simplified calculation, and actual replacement timing depends on when a specific electrode column reaches the required point for adding a new section (often determined by the remaining length above the holder). Maintenance schedules, planned downtime, and unscheduled events also influence the exact timing. The key point is that replacement is a continuous process in EAF operations. Operators continuously monitor electrode length and add new sections as needed, often multiple times per day, to maintain the operation of the electric furnace. Therefore, having a reliable supply of high-quality electrodes like those from a trusted graphite electrode factory is essential to avoid disruptions.
9. What’s Involved in the Safe Graphite Electrode Replacement Process?
Replacing a graphite electrode section – the process of adding a new electrode to the top of an existing column – is a critical procedure that demands precision, care, and adherence to safety protocols. Given the size and weight of the electrodes and the hazardous environment of the furnace, safety is the top priority. Improper handling or installation can lead to equipment damage, operational inefficiencies (like high resistance joints), or serious accidents. Mark Thompson, dealing with logistics and product quality, would appreciate the importance of proper procedures ensuring the product performs as expected from arrival to installation.
The typical process involves several steps:
-
Preparation:
- The new electrode section, complete with a pre-attached connecting nipple (or a nipple ready for insertion), is brought to the furnace area using appropriate lifting equipment (e.g., overhead crane with a specialized lifting bail that engages the electrode socket).
- The top socket of the existing electrode column in the furnace (the one needing replacement) is prepared. The power is switched off, and the electrode column is usually raised. Any remaining stub of the nipple from the previously consumed section might need to be removed.
- Crucially, both the socket threads on the existing electrode column and the nipple threads (and socket threads if nipple is separate) on the new electrode must be thoroughly cleaned. Compressed air is typically used to blow out any dust, graphite particles, or debris. Even small particles can interfere with proper mating and increase electrical resistance.
-
Joining ("Adding" the Electrode):
- The new electrode section is carefully lifted and positioned directly above the existing column.
- It is slowly lowered, ensuring perfect vertical alignment, so the nipple threads engage smoothly with the socket threads of the column below. Cross-threading must be avoided at all costs as it damages the graphite and prevents a secure connection.
- The new electrode is then rotated (usually mechanically) to tighten the connection.
-
Torquing:
- Once hand-tight (or machine-snug), a specialized, calibrated torque wrench system is used to apply the precise final tightening torque specified by the electrode manufacturer. This is perhaps the most critical step.
- Correct torque ensures optimal contact pressure between the electrode faces and nipple, minimizing electrical resistance and maximizing mechanical strength of the joint. Too little torque leads to overheating and loosening; too much torque can crack the electrode socket or nipple.
-
Final Checks:
- A visual inspection confirms the joint is properly seated and aligned.
- The lifting equipment is removed.
- The electrode column can then be lowered back into position, and furnace operation can resume once it’s safe.
Throughout this process, personnel must use appropriate Personal Protective Equipment (PPE), follow established safety procedures for working near the furnace and handling heavy loads, and ensure clear communication between the crane operator and the furnace floor crew. Proper training on removing electrodes and performing additions is essential. This meticulous process ensures the electrode functions correctly, electrical conductivity is maintained, and the risk of joint failure during the demanding smelt cycle is minimized.
10. Beyond Replacement: How Can You Optimize Electrode Life and Reduce Consumption?
While regular replacement of graphite electrodes is unavoidable, operators and managers can implement various strategies to optimize their lifespan and reduce the overall electrode consumption rate (kg/t). Minimizing consumption directly translates to lower operating costs, improved efficiency, and potentially reduced environmental impact. This requires a holistic approach, looking at everything from sourcing to furnace practices.
-
Source High-Quality Electrodes: Start with the right material. Partnering with a reliable manufacturer (like Allen’s factory in China) that produces electrodes (e.g., High-power graphite electrode) meeting consistent quality specifications (low resistance, high density, good thermal shock resistance, precise machining) provides a better foundation for performance. Ensure suppliers provide valid certifications (ISO standards, material specs), addressing Mark Thompson’s concern about certificate fraud.
-
Optimize Furnace Operations:
- Power Programs: Develop and utilize optimized power profiles tailored to the specific scrap mix and melting phase. Avoid excessive current densities.
- Arc Regulation: Train operators to maintain stable arcs and use automatic regulation systems effectively.
- Foamy Slag Practice: Master the art of creating and maintaining a good foamy slag layer to shield the electrodes from arc radiation and oxygen. This is often the single most effective operational change to reduce sidewall oxidation.
- Oxygen Control: Minimize air ingress into the furnace through effective sealing. Use process oxygen (lancing) judiciously and efficiently.
- Minimize Power-Off Time: Streamline operations to reduce tap-to-tap times, meaning less time the electrodes are under power (and consuming) per ton of steel.
-
Improve Handling and Installation:
- Careful Handling: Use appropriate lifting devices and avoid impacts during transport, storage, and installation to prevent cracks and damage. Store electrodes in a clean, dry place.
- Meticulous Jointing: Emphasize the importance of thorough cleaning of threads and sockets and precise torque application during electrode additions. This minimizes joint resistance and prevents failures.
-
Consider Protective Coatings: Some operations apply special refractory or antioxidant coatings the electrode sidewalls. These coatings act as a barrier, slowing down the rate of oxidation, particularly in the areas exposed to the hottest parts of the furnace atmosphere above the slag line. The effectiveness and cost-benefit need evaluation for each specific operation.
-
Regular Maintenance: Ensure timely maintenance of electrode holders, clamps, arms, and cooling systems. Good electrical contact at the holder is crucial to avoid energy loss and overheating. Promptly fix any water leaks in furnace cooling panels.
By implementing these measures, steelmakers can actively manage and reduce their graphite electrode consumption, moving it from an accepted, uncontrollable cost towards a manageable operational variable. This proactive approach not only saves money on electrodes but also contributes to more stable, efficient, and productive furnace operations.
Key Takeaways: Graphite Electrode Replacement
- Essential Function: Graphite electrodes are vital for conducting high electric currents to melt metal in electric arc furnaces due to their unique properties.
- Inevitable Consumption: Electrodes are consumables that wear down due to intense heat (tip sublimation), chemical reaction (oxidation on sidewalls), and potential physical damage (breakage, spalling).
- Efficiency Impact: Timely replacement is crucial for maintaining furnace efficiency, ensuring stable arc operation, minimizing energy consumption, and preventing costly downtime from electrode failure.
- Influencing Factors: Electrode consumption rates are affected by electrode quality, furnace operating parameters (voltage, current, oxygen use), slag practices, and scrap type.
- Operational Control: Careful handling, proper installation (cleaning and torquing joints), skilled operator control of the arc, and good maintenance significantly impact electrode life.
- Signs for Replacement: Watch for excessive tip wear, reduced diameter, visible cracks, spalling, joint overheating, or reaching a minimum stub length.
- Optimization Strategies: Reduce consumption by using high-quality electrodes, optimizing power programs and slag practices, minimizing air ingress, ensuring proper jointing, and potentially using protective coatings. Regular replacement must be part of a planned strategy.
Post time: 04-27-2025