As a procurement leader in the steel and metallurgy industry, you know that the efficiency and profitability of your operations hinge on the performance of your equipment. The electric arc furnace (EAF) is the heart of modern steelmaking, and the graphite electrode is its lifeblood. But this critical component is also a consumable that must be replaced regularly, impacting your bottom line. This article, written from my perspective as a factory insider with over two decades of experience, will demystify the graphite electrode. We’ll explore how it works, why it degrades, and most importantly, how you can make smarter purchasing decisions to maximize performance and minimize costs. This is the practical knowledge you need to navigate conversations with suppliers and optimize your furnace operations.
What is a Graphite Electrode and Why is it Essential?
Let’s start with the basics. A graphite electrode is a large, cylindrical column made from highly pure synthetic graphite. Think of it as a massive, high-tech pencil lead, but instead of writing, its job is to carry immense amounts of electricity. These electrodes are the primary heating element in an electric arc furnace (EAF) and ladle furnaces used in the steelmaking industry. Their primary function is to act as a powerful conductor, channeling electrical energy from an external power source into the furnace to melt raw materials.
The reason graphite is the material of choice is due to its unique combination of properties. First, it has excellent electrical conductivity, allowing it to handle the massive currents required for the melt without significant energy loss. Second, it possesses excellent thermal shock resistance. A graphite electrode can withstand incredible temperature changes—going from room temperature to the blistering heat inside a furnace (over 3,000°C or 5,400°F) without cracking. No other material can perform this task as efficiently and cost-effectively. This makes the graphite electrode indispensable for producing steel and other metals. The entire EAF process for making steel relies on the performance of this single graphite component.
The manufacturing of a graphite electrode is a complex process involving carefully selected raw material, primarily high-quality petroleum coke and needle coke. These materials are mixed, formed, baked, and then put through a lengthy graphitization process at extremely high temperatures. This final step aligns the carbon atoms into the ordered structure that gives graphite its signature properties. The quality of this process directly impacts the performance of the final electrode in the furnace.
How Do Graphite Electrodes Work in an Electric Arc Furnace (EAF)?
To understand the importance of the graphite electrode, you need to understand its role in the electric arc furnace steelmaking process. An EAF is essentially a giant kettle designed to melt scrap metal and other materials to produce new steel. The process begins when the roof of the furnace swings aside, and a large bucket loads it with scrap metal. Once loaded, the roof closes, and the graphite electrodes are lowered into the furnace until their tips are just above the scrap.
This is where the magic happens. A massive electrical current is sent through the graphite electrodes. When the tip of an electrode gets close enough to the scrap metal (or the molten bath), an electric arc jumps across the gap. This is the same principle as a bolt of lightning. The arc is a channel of superheated plasma that generates intense heat, reaching temperatures that can exceed 5000 degrees Fahrenheit. The job of the electrodes is to create an electric arc powerful enough to heat and melt tons of solid metal into a liquid state. The electrodes conduct this electricity to generate the required thermal energy.
The three graphite electrodes in a typical AC furnace work together to create a contained, stable heating zone. The intense heat from the arcs bores down through the scrap metal, creating a pool of molten steel at the bottom of the furnace. This process is incredibly fast and efficient, but it places extreme demands on the graphite electrode. The electrode must not only conduct electricity flawlessly but also withstand the brutal environment inside the EAF, which is filled with heat, chemical reactions, and mechanical stress. Using graphite electrodes is the only viable method for this kind of high-temperature smelt operation.
Why Must You Regularly Replace a Graphite Electrode in an EAF?
One of the most critical things for any procurement officer to understand is that a graphite electrode is a consumable item. It is not a permanent part of the furnace. From the moment it’s put into service, it begins a process of controlled degradation. This is by design. The extreme conditions required to melt steel mean that any material, including graphite, will be consumed. Therefore, you must replace the electrode periodically. This planned consumption is a fundamental operating cost of furnace steelmaking.
The concept of regular replacement can be a challenge. We all want equipment to last forever. However, the physics of the EAF process make this impossible for the electrode. The tip of the graphite electrode is subjected to the highest temperatures in the entire industrial process, causing the graphite to sublimate—turning directly from a solid into a gas. At the same time, the hot sides of the electrode are exposed to oxygen and other gases inside the furnace, causing them to oxidize or burn away.
This consumption means that the electrode column gets shorter and thinner with every batch of steel produced. To maintain the production process, operators must periodically add new graphite electrode segments to the top of the column. Understanding and managing this consumption rate is key to controlling costs and ensuring the furnace runs with high productivity. The reality is that these electrodes need to be replaced regularly to sustain the steel refining process.
What Are the Main Causes of Graphite Electrode Consumption?
The consumption of a graphite electrode in a furnace is not a simple matter of it “wearing out.” It’s a combination of several factors happening at once. As a buyer, knowing these causes helps you appreciate why high-quality matters and how furnace practices can impact your spending. There are two main categories of consumption: tip consumption and side consumption.
- Tip Consumption: This happens at the very end of the electrode where the arc is formed. The incredibly high-temperature of the electric arc causes the graphite to sublimate, meaning it turns directly from a solid into a gas. This is the primary mechanism that melts the scrap metal, but it also consumes the electrode tip. This is an unavoidable part of the process; you can’t melt the metal without it.
- Side Consumption (Oxidation): The body of the graphite electrode column glows red-hot due to the ambient heat in the furnace. This hot graphite surface reacts with oxygen (from air leaks or process gases) inside the EAF. This chemical reaction is called oxidation, and it literally burns away the sides of the electrode, making it thinner over time. This is similar to how a piece of charcoal burns in a grill. A significant portion of electrode loss comes from this side oxidation.
- Breakage and Spalling: This is a more catastrophic form of consumption. Thermal shock (heating or cooling too quickly) or mechanical stress (from shifting scrap or improper jointing) can cause pieces of the electrode or even entire sections to break off and fall into the molten bath. This not only wastes a valuable graphite electrode but can also introduce excess carbon into the steel, affecting the product quality. This is where the mechanical strength of the electrode becomes critical.
Understanding these factors shows that the life of a graphite electrode is a delicate balance. It must be strong enough to resist breakage, dense enough to resist oxidation, and conductive enough to do its job, all while being slowly consumed to smelt the metal.
How Does Furnace Atmosphere and Oxidation Impact Electrode Life?
Of all the factors that erode a graphite electrode, oxidation is one of the most significant and, to some extent, controllable. As I mentioned, graphite is a form of carbon. When hot carbon is exposed to oxygen, it will react to form carbon dioxide (gas). This reaction eats away at the electrode surface, reducing its diameter. The faster this happens, the shorter the life of your electrode.
The atmosphere inside the electric arc furnace is the main culprit. While operators try to seal the furnace, air inevitably leaks in around the doors, the roof, and other openings. This introduces oxygen that readily attacks the hot graphite column. Furthermore, some steelmaking practices, like oxygen lancing to refine the steel, can dramatically increase the amount of oxygen in the furnace, accelerating electrode consumption. The goal is to minimize this exposure as much as possible.
Modern EAF operations employ several strategies to combat oxidation. One common method is to create a “foamy slag” on top of the molten steel bath. This layer of slag acts like a blanket, covering the arc and the lower part of the electrode column, shielding them from the furnace atmosphere. Some plants also use water-cooled spray rings that create a curtain of water vapor around the electrode, or apply special refractory coatings to the graphite surface to protect it. By controlling the furnace atmosphere, a steel mill can significantly reduce its consumption of graphite electrodes per ton of steel produced, which has a direct impact on profitability.
RP, HP, UHP: What Do These Graphite Electrode Grades Mean for Your EAF?
When you look to source a graphite electrode, you will immediately encounter the terms RP, HP, and UHP. These are not just marketing labels; they represent different grades of graphite designed for different types of furnaces and power levels. Choosing the correct grade is absolutely critical for both performance and safety.
Grade | Full Name | Raw Material | Application |
---|---|---|---|
RP | Regular Power | Regular petroleum coke | Low-power furnaces, ferroalloy production, silicon metal. |
HP | High Power | Premium petroleum coke | High-power EAFs, ladle furnaces, general steelmaking. |
UHP | Ultra High Power | Primarily Needle Coke | The most demanding ultra-high power EAFs for large-scale steelmaking. |
- RP (Regular Power) Graphite Electrodes: These are the entry-level electrodes. Made from standard-grade petroleum coke, RP graphite electrodes are used in less demanding, lower-power applications like submerged arc furnaces for producing ferroalloys or silicon metal. Using an RP electrode in a high-power furnace would lead to rapid failure.
- HP (High Power) Graphite Electrodes: This is a step up in quality. HP electrodes are made from a better grade of raw material and have lower electrical resistance and better thermal shock resistance than RP graphite. They are the workhorses commonly used in many standard electric arc furnace operations for making steel.
- UHP (Ultra High Power) Graphite Electrodes: This is the premium grade. Ultra-high power graphite electrodes are made from a very high-quality, expensive raw material called needle coke. This material gives UHP graphite electrodes extremely low electrical resistance and a very low coefficient of thermal expansion. This means they can handle the highest current densities and the most extreme thermal shocks in the biggest and most powerful EAFs without failing. The performance of a uhp graphite electrode is essential for high-productivity steelmaking.
From my experience, I’ve seen clients try to save money by using an HP electrode in a UHP furnace. The result is almost always disastrous, leading to electrode breakage, production downtime, and higher overall costs. You must match the electrode grade to your furnace specifications.
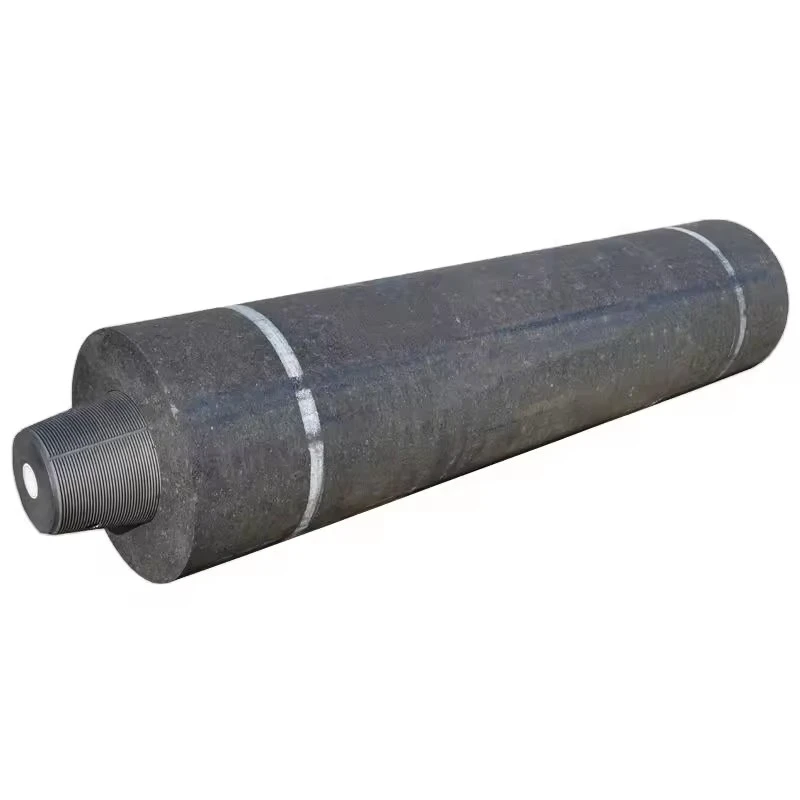
What Are Actionable Strategies to Minimize Graphite Electrode Consumption?
While graphite electrode consumption is unavoidable, it is not uncontrollable. For a procurement manager like Mark, driving down costs is always a priority. By working with your operations team, you can implement strategies that maximize the life of each electrode you purchase. The goal is to lower the kilograms of graphite consumed per ton of steel produced.
Here are some of the most effective strategies I have seen our most efficient customers use:
- Optimize Furnace Operations: This is the most impactful area. Techniques like creating a foamy slag to shield the electrode, minimizing air leaks into the furnace, and optimizing the power program can significantly reduce oxidation and tip consumption. It’s about running the furnace smartly.
- Proper Handling and Storage: A graphite electrode is more fragile than it looks. Dropping an electrode or bumping it can create micro-cracks that lead to failure under the stress of operation. They should be stored in a dry, clean area to prevent moisture absorption, which can cause problems in the furnace.
- Correct Jointing Technique: The electrode column is a series of segments connected by threaded graphite pins. This joint is a potential weak point. It is critical that the joint faces are perfectly clean and that the pin is torqued to the exact specification provided by the manufacturer. An under-tightened joint will overheat and fail, while an over-tightened one can crack the electrode.
- Minimize Thermal Shock: Avoid raising and lowering the electrodes too quickly, and try to maintain a steady production process. Rapid temperature changes create internal stress in the graphite, increasing the risk of cracking and spalling. This helps improve the overall energy consumption profile of the furnace.
By focusing on these areas, you can directly influence how long your purchased graphite products last, turning a simple purchase into a strategic investment in productivity.
As a Buyer, What Quality Markers Should I Look for in a Graphite Electrode?
For someone whose job is to source materials from overseas, ensuring quality is paramount. You’re right to be concerned about certifications and supplier integrity. When it comes to a graphite electrode, the specifications on paper must match the performance in your furnace. From my position at the factory, I can tell you what truly defines a high-quality electrode.
First, look at the key physical properties. The three most important are:
- Low Electrical Resistivity: This is a measure of how well the electrode conducts electricity. A lower number is better. It means less electrical energy is lost as heat within the electrode itself, and more power gets to the arc to melt the metal. This improves energy consumption.
- High Bulk Density: A denser electrode (with less internal pore space) is physically stronger and more resistant to oxidation. It will burn away more slowly, leading to a longer life in the furnace.
- High Flexural Strength: This measures the electrode’s ability to resist bending and breaking under mechanical stress, such as when scrap collapses against it in the furnace. Higher strength reduces the risk of costly breakage.
Second, inquire about the raw material. The quality of a graphite electrode is determined before it’s even formed. For HP and especially UHP graphite electrodes, the key ingredient is needle coke. Ask your supplier about the source and consistency of their needle coke. A reliable factory will have stable, long-term relationships with top raw material providers. A change in raw material can lead to a change in product quality. We also supply other high-quality carbon materials, like high performance pre baked anode carbon blocks, which rely on similarly stringent raw material controls.
Finally, demand verifiable certifications. An ISO 9001 certification is a basic requirement, but don’t stop there. Ask for a detailed Mill Test Certificate (MTC) with each shipment that lists the specific physical properties of the electrodes you are receiving. A trustworthy supplier will have no problem providing this and will stand by the data.
Why is the Precision of Graphite Rods and Joints So Critical?
We’ve talked about the main body of the electrode, but we can’t ignore the importance of the connecting pins and the machined threads. A typical electrode column in an EAF is made of several individual graphite rods (or segments) joined together. These joints are a critical point of potential failure.
Imagine the electrode column as a chain. It is only as strong as its weakest link, and the joints are often that link. The connecting pin and the sockets in the electrode ends are machined with high-precision threads. If these threads are not perfectly manufactured, the connection will be loose. A loose connection creates a small gap, which dramatically increases electrical resistance at that point. This resistance generates immense heat, causing the joint to overheat, glow, and eventually fail. This is a common cause of electrode breakage.
This is why, at our factory, we invest heavily in state-of-the-art CNC machining centers. The precision of the threading has a direct impact on the performance and safety of the entire graphite electrode column. The low thermal expansion properties of UHP graphite are also critical here, ensuring the joint remains tight even as the electrode heats up. When you source electrodes, ask about the supplier’s machining capabilities. Do they guarantee thread precision and provide clear instructions for joint assembly? This small detail can save you from a massive operational headache and ensure the reliability of components like our conductive graphite rod for electrodes.
How Can a Strong Supplier Partnership Improve My Entire Steelmaking Process?
In today’s global market, sourcing is about more than just finding the lowest price of graphite electrodes. It’s about building a partnership that adds value to your entire steelmaking process. As a procurement professional like Mark, you’ve likely experienced the pain points of poor communication, logistical nightmares, and questionable quality. A true partner helps you avoid these issues.
A reliable supplier acts as an extension of your team. They understand your specific furnace and production process. They can provide technical advice to help you select the right grade of graphite electrode and offer guidance on how to minimize consumption. This is the difference between a simple transaction and a strategic relationship. They won’t just sell you a graphite electrode; they’ll help you get the most out of it. This expertise extends to other graphite products as well, such as understanding the requirements for high strength graphite blocks or other specialty graphite materials.
Furthermore, a strong partner understands the importance of logistics and transparent communication. They provide accurate lead times, reliable shipping, and all the necessary documentation to ensure a smooth customs process. This prevents the costly shipment delays that can throw your production schedules into chaos. At the end of the day, a lower price on a carbon electrode is worthless if it breaks in the furnace or arrives a month late. Investing in a partnership with a proven, high-quality manufacturer is an investment in the stability and profitability of your own operations. The electrolysis process in aluminum smelting using a carbon anode is different, but the principle of supplier reliability is the same. The same goes for the carbon electrodes used in other applications.
Key Takeaways
- Graphite Electrodes are Essential Consumables: They are the critical heating element in an EAF, but they are designed to be consumed during the steelmaking process and need to be replaced regularly.
- Consumption has Multiple Causes: The life of a graphite electrode is affected by tip sublimation, side oxidation, and mechanical/thermal breakage.
Post time: 07-04-2025