Graphite electrodes are the unsung heroes of modern steel production, particularly within the electric arc furnace (EAF). These seemingly simple components play an indispensable role, acting as the conduit for immense electrical energy needed to melt scrap metal and refine it into high-quality steel. Understanding the function, types, and importance of the graphite electrode is crucial for anyone involved in EAF steelmaking, from furnace operators like Mark Thompson to procurement specialists seeking reliable, high-performance materials. This article dives deep into the world of graphite electrodes in electric arc furnaces, exploring why they are such a crucial component, how they work, the different grades available (HP and UHP), and what factors ensure optimal performance and efficiency in the demanding steelmaking process. We’ll explore why their high mechanical strength and unique properties make them essential for this high-temperature application.
What Exactly is an Electric Arc Furnace (EAF) and How Does it Differ from Traditional Methods?
An electric arc furnace (EAF) represents a significant advancement in steel production compared to traditional methods like the basic oxygen furnace (BOF) which primarily uses iron ore. The EAF is essentially a giant, powerful melting pot that utilizes electrical energy to transform scrap metal – ranging from old cars and appliances to industrial offcuts – into new steel. This process offers several advantages, notably its reliance on recycled raw material (scrap steel), which significantly reduces the environmental footprint compared to mining and processing virgin iron ore. EAFs are known for their flexibility, allowing steelmakers to produce a wide variety of steel grades, including specialized alloy steels.
The core difference lies in the energy source and primary raw material. While traditional blast furnaces rely on the chemical reactions of coke and iron ore at high temperature to produce molten iron (which is then refined into steel), the electric arc furnace uses high-power electrical current, delivered through graphite electrodes, to generate intense heat – we’re talking temperatures reaching up to 1,800 degrees Celsius (over 3,000 Fahrenheit) and beyond – directly melting the charged scrap metal. This method is generally faster for certain production scales and contributes to lower greenhouse gas emissions, making EAF steelmaking a more sustainable approach for the production of steel in many scenarios. It’s a powerhouse of recycling, turning yesterday’s metal into tomorrow’s infrastructure.
Why is the Graphite Electrode the Heart of the EAF Process?
The graphite electrode is truly indispensable in the electric arc furnace. Without it, the entire process simply wouldn’t work. Its primary job is to conduct the massive electrical current necessary to create an electric arc between the electrode tips and the metallic charge (scrap) inside the furnace. This arc is the source of the intense heat required to melt the scrap steel. Think of the graphite electrode as the element in a giant, super-powered kettle, but instead of boiling water, it’s melting tons of metal. Graphite electrodes are critical because they possess a unique combination of properties perfectly suited for this harsh environment.
Firstly, graphite boasts incredibly high electrical conductivity, allowing it to handle the enormous currents (tens of thousands of amperes) efficiently with minimal electrical energy loss (low resistivity). Secondly, it has exceptional thermal resistance and high mechanical strength, enabling it to withstand the extreme temperatures and thermal shock generated by the electric arc and the molten steel bath without rapidly degrading or breaking. Other materials would simply vaporize or shatter under such conditions. The role of graphite electrodes extends beyond just conducting electricity; they are a consumable electrode specifically designed for the extreme demands of the electric arc furnace steelmaking process. They are, without exaggeration, the functional core around which the EAF operates.
How Do Graphite Electrodes Work Within the Electric Arc Furnace? (Focus on the Arc)
The magic of the electric arc furnace happens when the graphite electrodes are lowered towards the charge of scrap metal. A high-voltage, high-amperage electric current is passed through the electrode column. As the electrode tips get close to the metallic charge, the air gap between them ionizes, creating a sustained electrical discharge – the electric arc. This arc is essentially a controlled bolt of lightning, releasing tremendous amounts of energy primarily in the form of heat. The electric current passes from one electrode, through the arc, into the scrap, potentially through another arc to another electrode (depending on the setup), completing the circuit.
This process of electric arc formation is continuous during the melting phase. The intense heat (often exceeding 3000°C within electric arc itself) radiates onto the scrap, rapidly causing it to melt. The electrodes conduct not just the current into the furnace, but also manage the arc‘s stability and position to ensure efficient melting. Sophisticated control systems adjust the position of the electrode columns constantly to maintain the optimal arc length and power input. It’s this controlled, high-energy arc, facilitated by the resilient graphite electrode, that forms the basis of heat generation in the electric arc furnace, enabling the transformation of solid scrap into molten metal.
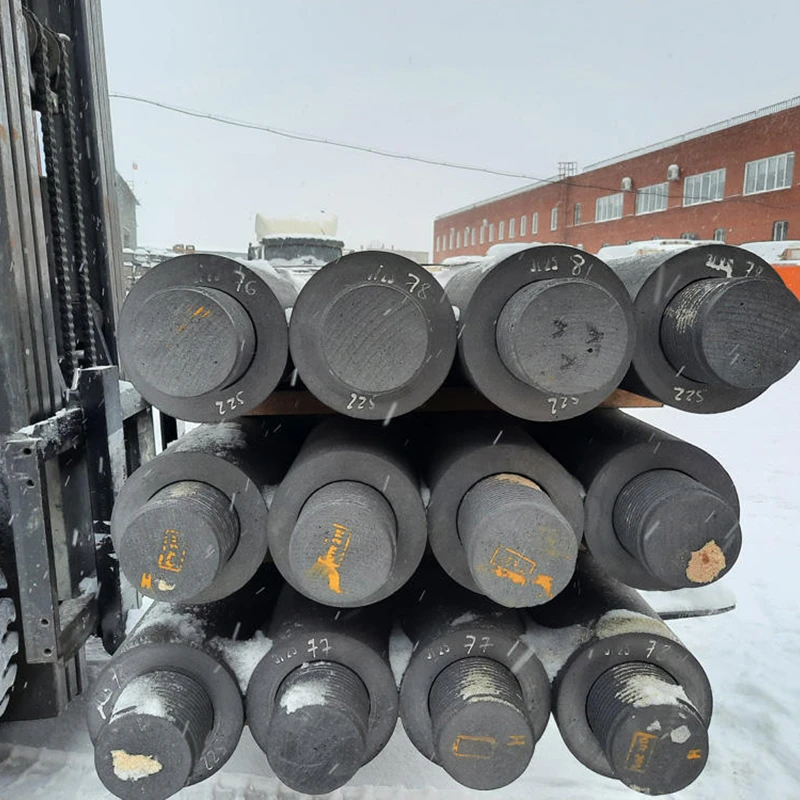
What are the Primary Functions of Graphite Electrodes in EAF Steelmaking?
The functions of graphite electrodes in an electric arc furnace are multifaceted and critical for successful furnace operation. While the primary function is well-known, several key roles highlight their importance:
- Conducting Electrical Current: This is the most obvious function. The electrode acts as the pathway for the massive electrical current needed to power the furnace. Their high electrical conductivity ensures this happens efficiently.
- Generating the Melting Arc: The electrode tips are specifically where the electric arc is struck. They must withstand the extreme temperatures and erosive forces of the arc itself to generate intense heat consistently. The ability of graphite electrodes to generate this heat necessary to melt the scrap is fundamental.
- Transferring Heat: The heat generated by the arc is transferred to the scrap charge primarily through radiation. The electrode‘s position and the arc stability influence how effectively this heat transfer occurs, directly impacting melting speed and energy consumption.
- Withstanding Harsh Conditions: The electrode must endure not only the high temperature of the arc and molten steel but also chemical attack from slag (molten impurities) and physical stresses during operation (like potential scrap cave-ins). Their thermal stability and high mechanical strength are vital here.
- Facilitating Refining: While melting is key, the arc also plays a role in the refine stage, helping to remove impurities and adjust the chemistry of the molten steel through controlled heat input and stirring effects induced by the arc.
In essence, the graphite electrode isn’t just a wire; it’s a high-performance tool engineered to deliver energy, create the melting arc, and survive one of the most extreme industrial environments on earth. The electrodes in electric arc furnace operations are truly the workhorses that melt steel.
What Goes into Making a High-Performance Graphite Electrode? (Raw Materials and Manufacturing)
Creating a graphite electrode capable of performing reliably in an electric arc furnace is a complex, multi-stage process involving carefully selected raw materials and precise manufacturing techniques. The primary ingredients are high-quality calcined petroleum coke and needle coke. Needle coke, with its highly crystalline, needle-like structure, is particularly crucial for high-performance electrodes (especially UHP graphite electrodes) because it provides excellent electrical conductivity, low thermal expansion, and superior resistance to thermal shock and oxidation.
The process typically involves:
- Mixing: Precisely measured amounts of calcined petroleum coke, needle coke, and a coal tar pitch binder are mixed at elevated temperatures.
- Forming (Extrusion or Molding): The mixture is then formed into the cylindrical shape of the electrode, usually through extrusion for standard sizes.
- Baking: The "green" electrode is slowly baked in a large furnace over several weeks to carbonize the binder and create a strong carbon structure.
- Impregnation: To increase density, strength, and conductivity, the baked electrode is often impregnated with pitch under pressure and then re-baked. This step might be repeated.
- Graphitization: This is a critical step. The electrode is heated to extremely high temperatures (approaching 3000 degrees Celsius) in a special electric furnace. This graphitization process rearranges the carbon atoms into the ordered crystalline structure of graphite, imparting the desired properties like high conductivity and thermal resistance. The graphitization temperature is carefully controlled.
- Machining: Finally, the graphitized electrode is precision-machined to create threaded sockets on the ends, allowing individual electrode sections to be joined together into longer columns for use in the EAFs.
This meticulous process ensures the final graphite electrode possesses the necessary characteristics – low resistivity, high density, excellent mechanical strength, and the ability to perform under the punishing conditions inside the furnace. As a factory owner with 7 production lines, I, Allen, can attest to the precision required at each step to produce high-quality steel components like these.
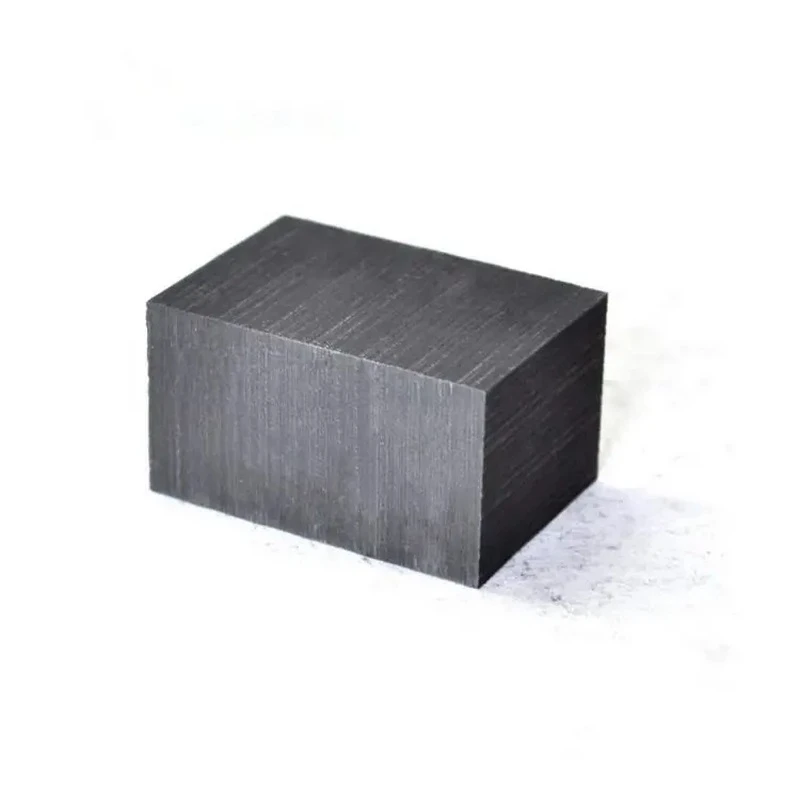
Decoding the Types of Graphite Electrodes: RP, HP, and UHP Explained
Not all graphite electrodes are created equal. They are generally classified into three types based on their properties and the power levels they are designed to handle in the electric arc furnace. Understanding these grades is essential for matching the electrode to the specific type of furnace and operational requirements.
-
Regular Power (RP) Graphite Electrode:
- Raw Materials: Primarily made from standard-grade calcined petroleum coke.
- Current Density: Designed for lower current density applications (typically < 18 A/cm²).
- Applications: Used in smaller or older EAFs, often for melting basic scrap steel or in ladle furnaces for refining, and sometimes in submerged arc furnaces for ferroalloy production. Our Regular Power Graphite Electorode is suitable for these applications.
- Characteristics: Lower cost, moderate strength and conductivity compared to higher grades. An RP graphite electrode is the entry-level option.
-
High Power (HP) Graphite Electrode:
- Raw Materials: Uses higher quality calcined petroleum coke, sometimes with a portion of needle coke.
- Current Density: Suitable for higher current density operations (typically 18-25 A/cm²).
- Applications: Used in medium to large capacity EAFs for steelmaking process requiring faster melting times than RP allows.
- Characteristics: Offers better electrical conductivity, thermal resistance, and mechanical strength than RP electrodes. A reliable choice for many standard EAFs. Check out our High-power graphite electrode options.
-
Ultra-High Power (UHP) Graphite Electrode:
- Raw Materials: Primarily made from premium needle coke.
- Current Density: Designed for the most demanding applications with very high current density (> 25 A/cm²).
- Applications: Essential for modern, high-productivity EAFs aiming for maximum output and efficiency. Used to melt high volumes of scrap quickly.
- Characteristics: Superior electrical conductivity (low resistivity), excellent resistance to thermal shock and oxidation, highest mechanical strength. UHP graphite electrodes allow furnaces to operate at peak power levels, reducing tap-to-tap times. Our premium Ultra-high power graphite electrode is engineered for these demanding tasks.
Choosing the correct electrode type (RP, HP, or UHP) is vital for optimizing furnace operation, managing energy consumption, and controlling overall production costs. Using an electrode not rated for the furnace’s power can lead to premature failure and inefficiency.
How Does the Quality of an Electrode Impact EAF Performance and Overall Costs?
The quality of the graphite electrode used in an electric arc furnace has a direct and significant impact on both the performance of the furnace and the overall cost of steel production. For procurement officers like Mark Thompson, understanding this link is key to making cost-effective decisions that don’t compromise operational efficiency. Lower-quality electrodes might seem cheaper upfront, but they often lead to higher overall costs due to increased consumption rates (breaking or oxidizing faster), longer melting times (due to lower conductivity or instability), and potential operational disruptions.
High-quality graphite electrodes, characterized by uniform structure, high density, low resistivity, excellent thermal shock resistance, and high mechanical strength, contribute to:
- Lower Electrode Consumption: They withstand the extreme temperatures and mechanical stresses better, leading to a longer service life and less graphite being consumed per ton of steel produced.
- Improved Energy Efficiency: Better electrical conductivity means less electrical energy is wasted as heat within the electrode itself, allowing more power to reach the arc and melt the scrap faster.
- Increased Productivity: Stable arc performance and reduced downtime due to electrode breakage or premature failure lead to shorter tap-to-tap times and higher furnace output.
- Reduced Risk of Breakage: Superior mechanical strength minimizes the risk of electrode columns breaking during operation, which can cause costly delays and potential furnace damage.
- Consistent Performance: Reliable electrodes provide predictable melting behaviour, allowing for better process control and helping produce high-quality steel consistently.
Conversely, inconsistent or low-quality electrodes can lead to frequent breaks, higher energy use, unpredictable melt cycles, and increased slagging issues, ultimately driving up the cost per ton of steel. Therefore, investing in quality graphite electrodes is crucial for efficient and economical EAF steelmaking.
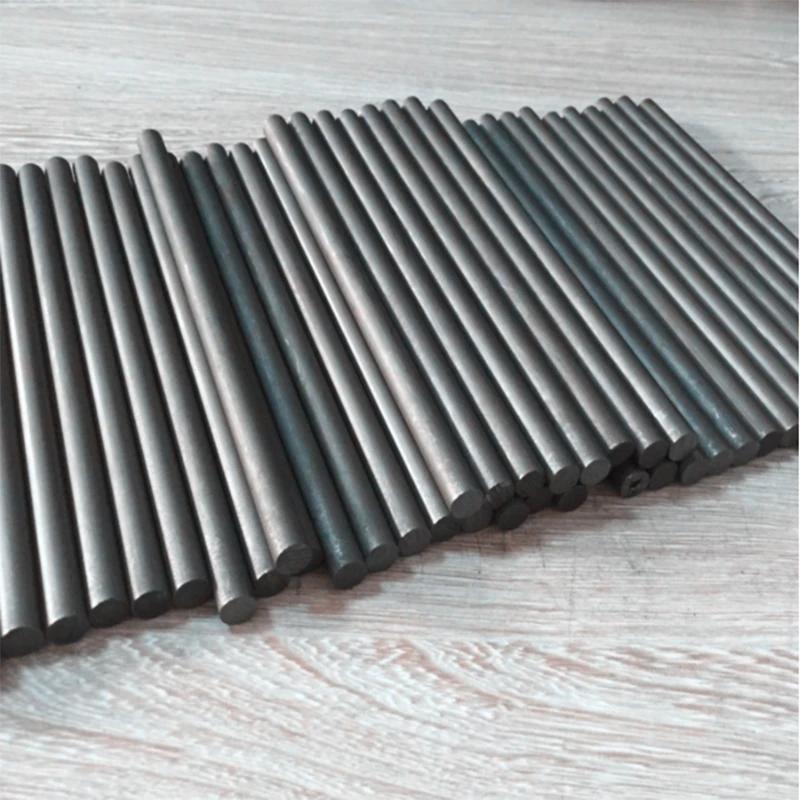
What Key Challenges Do Steelmakers Face with Graphite Electrodes in EAF Operations?
Operating an electric arc furnace comes with inherent challenges, and several of these relate directly to the graphite electrodes. Steelmakers and furnace operators constantly strive to mitigate these issues to ensure smooth and efficient production. One major challenge is electrode consumption. Graphite electrodes are used up during the process through tip sublimation (vaporization due to the arc‘s intense heat), surface oxidation (reacting with air and furnace gases), and mechanical breakage or spalling. Managing and minimizing this consumption is critical for cost control.
Another significant challenge, often a pain point for purchasers like Mark, is ensuring consistent electrode quality and reliability. Variations in electrode properties can lead to unpredictable performance, unstable arc behaviour, and increased risk of breakage. This underscores the importance of sourcing from reputable manufacturers with strong quality control. Handling and joining electrode sections also require care; improper jointing can lead to high electrical resistance at the connection, generating excess heat and potentially causing joint failure or electrode breakage. Furthermore, electrode breakage during operation is a major headache, causing significant downtime, potential damage to the furnace lining, and loss of production. Finally, market price volatility for graphite electrodes, driven by raw material costs (especially needle coke) and global supply/demand, adds another layer of complexity to procurement and cost management for EAFs.
As a Buyer (like Mark), How Can You Ensure You Source Reliable and High-Quality Graphite Electrodes?
For company owners and procurement officers like Mark Thompson, sourcing reliable, high-quality graphite electrodes is paramount. Given the potential pain points of inconsistent quality, shipment delays, and even certificate issues, a strategic approach to supplier selection and verification is essential. Here are key steps buyers can take:
- Thorough Supplier Vetting: Don’t just rely on price. Research potential suppliers. Look for established factories with a proven track record, like our facility in China with 7 production lines. Check their experience, main export markets (experience with USA, Europe, etc., indicates familiarity with international standards), and production capabilities.
- Request Certifications and Test Reports: Ask for detailed specifications, material analysis reports, and relevant certifications (e.g., ISO 9001 for quality management). While vigilance against fraud is needed, legitimate suppliers readily provide comprehensive documentation for their electrode products. Query any discrepancies.
- Understand the Grades (RP, HP, UHP): Ensure the supplier clearly differentiates between types of graphite electrodes and can provide the specific grade (HP or UHP) required for your electric arc furnace. Discuss the raw material base (e.g., proportion of needle coke for UHP graphite).
- Inquire about Quality Control: Ask about their QC processes throughout manufacturing – from raw material inspection to graphitization control and final electrode machining and testing. How do they ensure consistency?
- Discuss Logistics and Lead Times: Clearly communicate your required delivery schedules. Reliable suppliers understand the impact of delays and should provide realistic lead times and have robust logistics arrangements. Address potential shipment issues proactively.
- Seek References or Case Studies: Reputable manufacturers often have testimonials or case studies from satisfied customers, potentially even in your region (USA, North America, Europe).
- Consider a Factory Audit or Third-Party Inspection: For significant purchases or new supplier relationships, arranging an audit or pre-shipment inspection can provide extra assurance regarding quality and processes.
- Build a Relationship: Open communication is key. Work with suppliers who are responsive, transparent, and willing to understand your specific needs regarding graphite electrodes in EAF operations. As Allen, I prioritize clear communication with clients like Mark.
By taking these steps, buyers can significantly improve their chances of sourcing high-quality electrodes used in EAF operations, minimizing risks and ensuring reliable furnace performance. Products like our Conductive graphite rod for electrodes and high-strength graphite blocks reflect our commitment to quality materials.
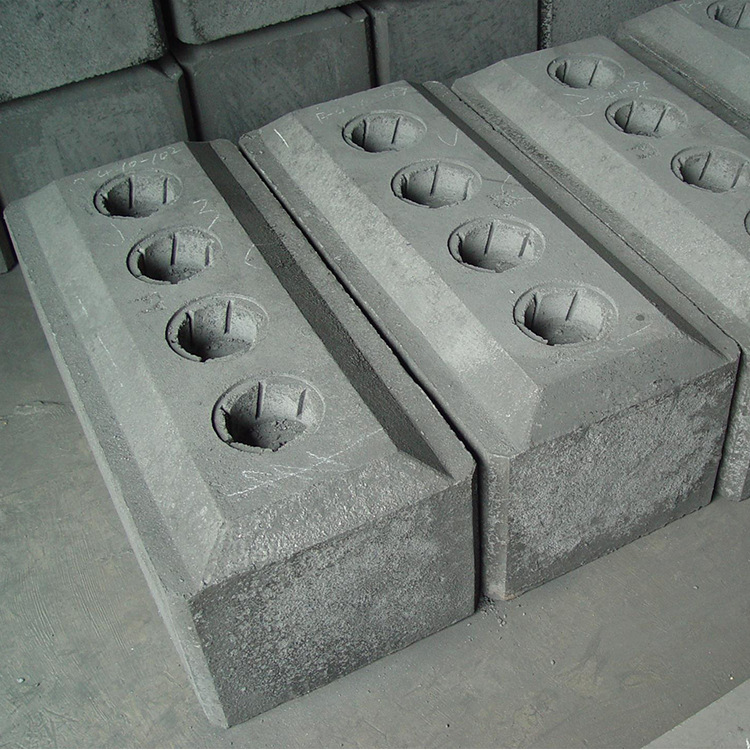
Looking Ahead: The Evolving Role of Graphite Electrodes in Sustainable Steel Production
The electric arc furnace method, heavily reliant on graphite electrodes, is already a cornerstone of greener steel production due to its ability to recycle scrap steel. As the global push for sustainability intensifies, the role of graphite electrodes and EAF steelmaking is set to become even more important. Future developments will likely focus on further enhancing the efficiency and reducing the environmental impact of this process. This includes ongoing research into electrode materials and coatings to reduce oxidation and lower consumption rates, directly impacting operational costs and resource usage.
Furthermore, innovations in EAF technology itself, such as improved process control, enhanced energy recovery systems, and the potential use of renewable electrical energy sources to power the arc, will complement advances in electrode technology. The drive towards higher current density operations to maximize productivity will continue to demand improvements in UHP graphite electrode quality, particularly concerning thermal shock resistance and mechanical strength. As we move forward, the synergy between efficient furnace design and high-performance graphite electrodes will be crucial in making steel production more sustainable, reducing reliance on traditional blast furnaces, and contributing to a circular economy by effectively recycling scrap metal. The humble graphite electrode will remain an indispensable component in the future of modern steel.
Key Takeaways: Graphite Electrodes in EAF Steelmaking
- Indispensable Component: Graphite electrodes are essential for electric arc furnace (EAF) operation, conducting the electric current needed to create an electric arc and melt scrap metal.
- Unique Properties: Graphite is chosen for its high electrical conductivity, exceptional thermal resistance to withstand the extreme temperatures, and high mechanical strength required in the harsh EAF environment.
- How They Work: Electrodes carry high current passes to generate an arc between the electrode tip and the scrap, producing intense heat for melting.
- Types Matter: Electrodes come in grades – Regular Power (RP), High Power (HP), and Ultra-High Power (UHP) – based on raw materials (petroleum coke, needle coke) and current density capacity. Matching the electrode type to the furnace is crucial.
- Quality Impacts Costs: High-quality graphite electrodes lead to lower consumption, better energy efficiency, increased productivity, and reduced operational risks compared to lower-quality options.
- Sourcing Strategically: Buyers should vet suppliers thoroughly, verify certifications, understand electrode grades, inquire about QC, and discuss logistics to ensure reliable sourcing.
- EAF is Greener: EAF steelmaking, powered by graphite electrodes, plays a key role in recycling scrap steel and offers a more sustainable alternative to traditional methods.
- Future Focus: Ongoing development aims to improve electrode efficiency (lower consumption, higher performance) and integrate with advancements in sustainable EAF technology.
Post time: 05-06-2025