Graphite electrodes are vital components in various industrial processes, most notably in electric arc furnaces (EAF) for steel production and in diverse electrochemical applications. The condition of the electrode surface directly impacts performance, efficiency, and longevity. A contaminated or improperly maintained electrode can lead to increased consumption, erratic performance, and even catastrophic breakage. This guide provides comprehensive instruction on how to properly clean and maintain your graphite electrode surfaces, drawing from practical factory insights. Whether you’re an EAF operator like Mark Thompson, concerned about quality and cost-efficiency, or a scientist preparing for precise electrochemical measurements, understanding these procedures is crucial for optimal results. Let’s explore why a clean electrode matters and how to achieve it.
1. Why is a Clean Graphite Electrode Surface Crucial for Performance?
The performance of a graphite electrode is intrinsically linked to its surface condition. In high-temperature applications like electric arc furnaces, a clean surface ensures optimal electrical conductivity. Contaminants act as insulators, increasing electrical resistance. This forces the system to draw more power to achieve the same melting temperature, leading to higher energy consumption and reduced efficiency – a key concern for cost-conscious operators. Furthermore, uneven current distribution caused by surface fouling can create localized hot spots, increasing thermal stress and the risk of breakage or premature wear.
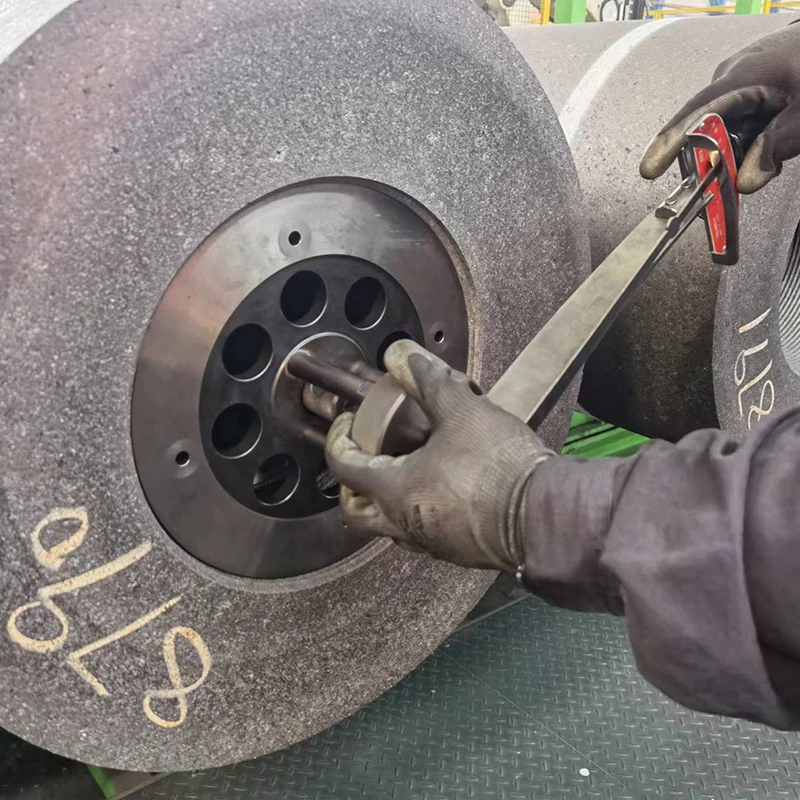
Beyond EAFs, in electrochemical applications, the surface of the electrode is where the action happens – it’s the critical interface between the electrode material and the electrolyte. Contaminants can block active sites, alter reaction pathways, or introduce unwanted side reactions. This directly impacts the accuracy and reproducibility of measurements. For instance, in voltammetry, a dirty working electrode surface can lead to distorted peak shapes, shifted peak potentials, and reduced signal intensity, making it difficult to accurately determine analyte concentration or study reaction mechanisms. A clean electrode surface is fundamental for obtaining reliable electrochemical data. Maintaining a pristine electrode surface ensures that the measured electrochemical response truly reflects the process under investigation.
The integrity of the connection points, specifically the thread sections where two electrodes join via a nipple, is also paramount. Contaminants like dust or grease in the thread can impede current flow and lead to overheating at the joint. This is a common point of failure, often resulting in loosening, increased electrical resistance, or even breakage. Ensuring both the main body surface and the connecting thread areas are meticulously clean is vital for the structural and electrical integrity of the entire electrode column, especially when dealing with large-diameter electrodes demanding high torque during assembly.
2. What Contaminants Typically Foul Graphite Electrode Surfaces?
Graphite electrode surfaces can become contaminated through various stages – during storage, handling, and operation. Understanding the common culprits helps in selecting the appropriate cleaning methods. One major source is oil and water residues, often transferred from handling equipment or personnel hands. Dust and particulate matter from the storage environment or the plant atmosphere can easily settle on the surface, especially within the porous structure of some graphite types. These might seem minor, but even a thin layer can significantly impact performance.
During operation, particularly in EAFs, graphite electrodes are exposed to harsh conditions. Slag splash, metallic deposit particles, and oxidized material can adhere firmly to the electrode surface. These process-related contaminants are often harder to remove and can significantly alter the electrode’s electrical and thermal properties. In electrochemical settings, contaminants can originate from the electrolyte itself (impurities, degradation products), reference electrode leakage, or adsorption of molecules from the sample matrix onto the electrode surfaces. These adsorbed species can passivate the electrode, hindering electron transfer.
It’s also important to consider residues from previous cleaning attempts or manufacturing. Improperly rinsed cleaning agents or residual polishing materials (like alumina or diamond paste used in electrochemical electrode preparation) can themselves act as contaminants. Even the adhesive from protective tape used on electrode threads can leave a sticky residue if not removed properly. Therefore, a thorough cleaning procedure must account for removing not just external dirt but also any potential residue from the cleaning process itself. We must analyze the potential sources of fouling to choose the best cleaning strategy.
3. Essential Tools and Materials for Effective Electrode Cleaning?
Having the right tools and materials on hand makes the cleaning process safer and more effective. The specific items needed may vary slightly depending on the electrode type and application (EAF vs. electrochemical cell), but a basic kit should include:
- Safety Gear: Always prioritize safety. This includes appropriate gloves (e.g., nitrile or neoprene to resist solvents) and safety glasses or goggles to protect against splashes and airborne particles.
- Brushes: Soft-bristled brushes (like nylon) are generally preferred for routine cleaning to avoid scratching the graphite electrode surface. A wire brush (preferably brass, softer than steel) might be used cautiously for removing very stubborn deposits on industrial electrodes, but never on delicate electrochemical electrodes. Specific thread cleaning brushes are also recommended.
- Cloths: Lint-free wipes or cloth (like microfiber) are essential for wiping surfaces without leaving behind fibers. Standard paper towels should be avoided.
- Solvents: The choice of solvent depends on the contaminant.
- Isopropyl alcohol (IPA) or acetone are common choices for removing grease, oil and water. Always check for compatibility with the specific graphite electrode grade and downstream application (especially in sensitive electrochemical experiment work).
- Deionized (DI) water or distilled water is crucial for rinsing, particularly in electrochemical applications, to avoid introducing ionic contaminants.
- Compressed Air: A source of clean, dry compressed air is invaluable for blowing away loose dust and debris, and for drying the electrode after washing. Ensure the air supply is free of oil.
- Polishing Materials (for Electrochemical Electrodes): For preparing electrochemical electrodes, various grades of polishing media are needed, such as:
- Alumina slurries (e.g., 1.0 μm, 0.3 μm, 0.05 μm)
- Diamond pastes/sprays (similar range of particle sizes)
- Polishing pads (emery cloth is generally too coarse, specific polishing cloths are used)
- Containers: Clean beakers or trays for holding solvents during washing or ultrasonic cleaning.
Here’s a quick reference table:
Item | Purpose | Notes |
---|---|---|
Safety Glasses | Eye protection | Mandatory |
Gloves | Hand protection, prevent contamination | Solvent-resistant (e.g., nitrile) |
Soft Brush | Remove loose debris | Avoid scratching the surface |
Lint-Free Cloth | Wiping, applying solvent | Prevents fiber contamination |
Compressed Air | Blow off dust, drying | Must be clean and oil-free |
Isopropyl Alcohol | Degreasing, general cleaning | Good general-purpose solvent |
Acetone | Stronger degreasing | Check compatibility, more volatile |
DI Water | Rinsing (esp. electrochemical) | Prevents ionic contamination |
Ultrasonic Bath | Deep cleaning (optional/specific) | Use with appropriate solvent |
Polishing Kit | Electrochemical electrode preparation | Alumina/diamond, pads |
Thread Caps/Tape | Protect thread during cleaning/storage | Prevents damage |
Selecting the right tools is the first step towards a properly cleaned graphite electrode.
4. Step-by-Step Guide: How to Safely Wash and Clean Graphite Electrodes?
Cleaning graphite electrodes, whether large ones for furnaces or small ones for labs, requires a methodical approach. Here’s a general procedure, which you can adapt based on the electrode size and contamination level:
- Initial Inspection & Safety: Put on your safety glasses and gloves. Carefully inspect the electrode for any visible damage, cracks, or severe contamination. Check the thread areas specifically.
- Dry Cleaning: Use clean, oil-free compressed air to blow off any loose dust and particulate matter from the entire surface, including the threads. A soft brush can help dislodge lightly adhered particles. Work in a well-ventilated area.
- Solvent Wipe (if needed): If greasy residues (oil and water) are present, moisten a lint-free cloth with an appropriate solvent (like isopropyl alcohol). Gently wipe the contaminated areas. Avoid soaking the electrode, especially porous types, unless intentionally performing a bulk wash. Wipe from the cleaner areas towards the dirtier areas. For threads, use a dedicated thread brush or cloth wrapped around a tool to clean the grooves.
- Stubborn Deposits (Industrial Electrodes): For heavily fouled industrial electrodes (e.g., EAF electrode with slag), mechanical cleaning might be necessary before washing. This could involve careful scraping with a non-metallic tool or gentle use of a brass wire brush. Extreme caution is needed to avoid damaging the electrode surface. This step is generally not applicable to delicate electrochemical electrodes.
- Rinse: If solvents were used, or for general washing, rinse the electrode thoroughly. For electrochemical electrodes, use high-purity DI water or the same high-purity solvent used for cleaning. For industrial electrodes, depending on the cleaning agent and process needs, a water rinse followed by ensuring complete dryness might suffice. The goal is to remove all traces of the cleaning agent and dislodged contaminants. Multiple rinses might be necessary.
- Drying: Allow the electrode to air dry completely in a clean environment. You can accelerate drying using compressed air (ensure it’s clean). Gentle heating (e.g., in an oven below 100 °C) can be used, but avoid excessive temperatures that could oxidize or thermally shock the graphite. The electrode must be fully dry before storage or use, especially before connecting joints or immersing in an electrolyte. A typical air-drying time might be 30 min to several hours, depending on size and porosity. The electrode should be allowed to dry thoroughly.
- Final Inspection: Once dry, perform a final visual inspection to ensure the surface is uniformly clean and free from residues or damage. Check the threads again.
This systematic approach ensures that the graphite electrode is effectively cleaned while minimizing the risk of damage. Remember to handle the electrode carefully throughout the process.
5. What is the Role of Ultrasonic Cleaning for Graphite Electrodes?
Ultrasonic cleaning offers a more intensive cleaning method compared to simple wiping or brushing. It utilizes high-frequency sound waves to create cavitation bubbles within a liquid solvent. These bubbles implode near the electrode surface, generating tiny, powerful jets and localized pressure changes that dislodge contaminants from the surface, including pores and intricate features like threads. Think of it as a microscopic scrubbing action.
This method is particularly effective for removing stubborn, fine particulate matter, residues lodged in surface porosity, or contaminants in hard-to-reach areas like the root of a thread. For electrochemical electrodes, an ultrasonic wash (typically 5-15 min) in an appropriate solvent (like DI water or isopropanol) after initial polishing or between experiments can significantly improve surface cleanliness and ensure a more active, reproducible electrode surface. It’s a common step in rigorous cleaning protocols aiming for pristine electrode surfaces.
However, ultrasonic cleaning should be used judiciously. The intense energy can potentially cause surface damage or erosion, especially with softer graphite grades or prolonged exposure times. It’s crucial to:
- Select an appropriate solvent compatible with the graphite and the contaminants.
- Control the duration (start with short times, e.g., 2 minutes to 5 min, and increase only if necessary).
- Ensure the electrode doesn’t directly rest on the bottom of the ultrasonic bath (use a holder or suspend it).
- Rinse thoroughly after the ultrasonic step to remove dislodged debris and residual solvent.
Ultrasonic cleaning is a powerful tool in the electrode cleaning arsenal, but it’s not always necessary or appropriate. Evaluate the type of contamination and the sensitivity of the electrode before employing this technique. For many routine cleaning tasks, manual methods described earlier are sufficient.
6. How Do You Prepare Electrodes for Electrochemical Experiments?
Preparing an electrode for an electrochemical experiment requires meticulous attention to surface cleanliness and condition, as even trace impurities can drastically affect results. The goal is to achieve a smooth, reproducible, and active surface. The exact procedure depends on the electrode material (e.g., glassy carbon, graphite paste, pyrolytic graphite) and the specific experiment, but generally involves polishing, cleaning, and sometimes electrochemical pre-treatment.
A typical preparation sequence for a solid graphite electrode (like glassy carbon) might look like this:
- Mechanical Polishing: This step aims to remove any previous contaminants or passivated layers and create a fresh, smooth surface.
- Start with coarser polishing media (e.g., 1 μm alumina or diamond paste) on a polishing cloth. Polish in a figure-eight motion for 1-2 minutes.
- Rinse thoroughly with DI water.
- Move to finer polishing media (e.g., 0.3 μm, then 0.05 μm alumina). Polish for 1-2 minutes with each grade.
- Rinse thoroughly with DI water between each step.
- Ultrasonic Cleaning: After polishing, place the electrode tip in a beaker with DI water (or sometimes ethanol/isopropanol) and sonicate for several min (e.g., 5 min) to remove polishing debris trapped in microscopic crevices.
- Final Rinse: Rinse extensively with high-purity DI water. Some protocols might involve a final rinse with the electrolyte to be used in the experiment.
- Electrochemical Pre-treatment (Optional): Depending on the application, the electrode might require electrochemical activation or cleaning. This often involves cycling the potential within a specific range in the supporting electrolyte. This step can help remove residual oxides or adsorbed species and stabilize the electrode surface. The exact potential range and cycle parameters are specific to the electrode material and the electrolyte system. The aim is often to achieve a stable, low background current and well-defined electrochemical peak responses for known redox couples (like ferrocene or potassium ferricyanide) as a check of electrode activity.
- Drying (if needed): If the electrode is not used immediately, it should be dried carefully (e.g., with a gentle stream of nitrogen or argon) and stored properly.
The quality of the electrochemical cell setup, including the reference and counter electrodes, and the purity of the electrolyte and solvents, are equally crucial. A perfectly prepared working electrode won’t yield good data if other components are faulty or contaminated. Achieving a sharp, well-defined electrochemical peak with the expected potential is often a key indicator of a properly prepared electrode and cell.
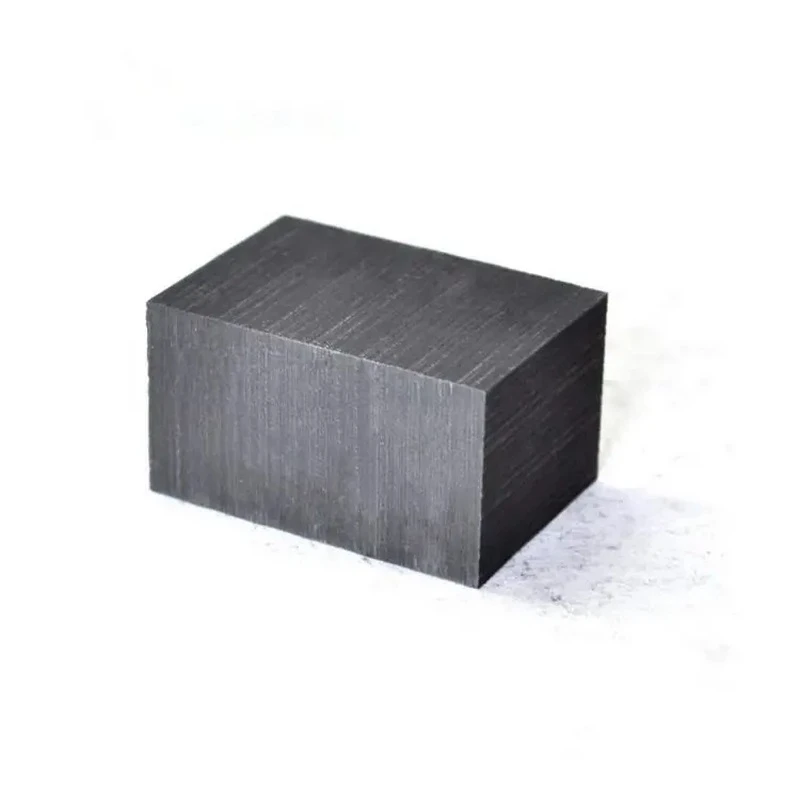
7. Preventing Damage: What Are Key Precautions During Electrode Cleaning?
While cleaning is essential, improper techniques can cause more harm than good. Graphite, despite its high-temperature resilience, can be brittle and susceptible to mechanical damage. Here are key precautions to take:
- Avoid Excessive Force: Never use excessive force when brushing, wiping, or handling the electrode. Graphite can scratch or chip. Use soft brushes and lint-free cloths. Avoid dropping or impacting the electrode, as this can lead to catastrophic breakage.
- Protect Threads: The thread sections are critical for connection and current transfer but are also vulnerable.
- Always clean threads carefully, ensuring no debris remains.
- Use protective caps or tape over threads during vigorous cleaning of the main body or during storage/transport to prevent the electrode threads from damage.
- When connecting two electrodes, ensure threads are aligned correctly before tightening. Use the recommended torque specification – overtightening can stress the thread and lead to breakage later, while under-tightening can cause loosening and overheating. Use a proper holder or clamp during assembly/disassembly. Avoid using steel tools directly on the graphite if possible, or use them with extreme care.
- Chemical Compatibility: Ensure any solvents or cleaning agents used are compatible with the specific grade of graphite electrode and won’t leave harmful residues for the intended application. This is especially critical for high-purity graphite or electrochemical applications where even trace contaminants matter. Always rinse thoroughly.
- Thermal Shock: Avoid rapid temperature changes. Don’t take a hot electrode and immerse it in cold cleaning liquid, or heat a wet electrode too quickly. Gradual temperature changes are key to preventing thermal stress and cracking (breakage). If you need to bake an electrode dry, use a moderate temperature (e.g., < 100-120 °C) and allow for gradual heating and cooling.
- Ultrasonic Cautions: As mentioned earlier, limit the duration and intensity of ultrasonic cleaning to avoid pitting or eroding the electrode surface.
By adhering to these precautions, you can effectively clean your graphite electrodes without compromising their structural integrity or performance. Preventing damage is just as important as removing contaminants.
8. How to Inspect and Verify Electrode Cleanliness Post-Wash?
After cleaning, how do you know if the electrode is actually clean enough? Verification is an important step, especially in critical applications. The methods range from simple visual checks to more sophisticated surface analysis techniques.
For general industrial electrodes (like EAF electrodes), a thorough visual inspection is the primary method. Look for:
- Uniform Appearance: The surface should look uniformly clean, without patches of discoloration, residue, or visible contaminants like oil sheen or dust clumps.
- Thread Condition: Pay close attention to the thread grooves and faces. They should be free of debris, grease, and damage.
- Wipe Test: Gently wipe a small area of the cleaned, dry surface with a clean, white, lint-free cloth. The cloth should remain clean, indicating no loose residue is transferring.
For electrochemical electrodes, where surface condition is paramount, verification is often more rigorous:
- Visual Inspection (Microscopic): Inspecting the polished surface under magnification can reveal scratches, pits, or residual polishing material.
- Electrochemical Testing: Running a cyclic voltammogram (CV) in a standard electrolyte solution containing a well-behaved redox couple (e.g., 1 mM potassium ferricyanide in 0.1 M KCl) is a common diagnostic tool. A properly cleaned and activated electrode should exhibit:
- A low background current.
- Well-defined oxidation and reduction peak shapes.
- The expected peak separation (ΔEp), which is theoretically close to 59/n mV at room temperature for a reversible n-electron process. Deviations often indicate a sluggish or contaminated surface.
- Reproducible scans upon repeated cycling.
- Contact Angle Measurement: The way a droplet of water or electrolyte beads up (or spreads out) on the electrode surface can provide insight into its cleanliness and hydrophobicity/hydrophilicity, which can be sensitive to surface contaminants.
- Surface Spectroscopic Techniques (Advanced): In research settings, techniques like X-ray Photoelectron Spectroscopy (XPS) or Raman Spectroscopy might be used to analyze the elemental composition and chemical state of the electrode surface, confirming the absence of specific contaminants. This level of analytical detail is usually reserved for R&D.
Regular inspection and verification, appropriate to the application, ensure that the cleaning process is effective and that the graphite electrode is ready for optimal performance. This helps prevent costly failures or inaccurate measurement results.
9. Maintaining Cleanliness: How to Properly Store and Handle Graphite Electrodes?
Cleaning graphite electrodes is essential, but preventing contamination in the first place is even better. Proper storage and handling procedures are crucial to maintain cleanliness and prevent damage. Here are some best practices:
- Clean and Dry Storage: Store electrodes in a clean, dry environment, away from dust, moisture, chemical fumes, and potential physical impacts. Avoid storing them directly on the floor. Use designated racks or pallets.
- Protective Packaging: Keep electrodes in their original protective packaging for as long as possible. For industrial electrodes, this often includes wrapping and cushioning. Nipples (connecting pins) should also be stored carefully, often in dedicated boxes.
- Thread Protection: Always use protective caps or plugs on electrode and nipple threads during storage and handling. This prevents both contamination and physical damage to these critical areas. Ensure the caps themselves are clean. Tape can be used as a temporary measure but ensure it doesn’t leave adhesive residue.
- Handling:
- Always use clean lifting equipment (slings, clamps, holder devices). Ensure lifting equipment doesn’t introduce grease or dirt. Specific lifting plugs that screw into the electrode socket are often used for large electrodes.
- Minimize handling. Plan movements to avoid unnecessary relocation.
- Personnel handling electrodes should wear clean gloves to prevent transferring oil and water or dirt from their hands.
- Segregation: If possible, store new electrodes separately from used or partially consumed ones to prevent cross-contamination.
- Environment Control: In sensitive applications (like cleanrooms for electrochemical work or semiconductor processing), maintain strict environmental controls to minimize airborne particulates.
Implementing these simple yet effective storage and handling procedures can significantly reduce the need for intensive cleaning, prolong electrode life, ensure consistent performance, and prevent costly breakage or operational issues. As a factory owner (like myself, Allen), we emphasize these practices internally and recommend them strongly to our customers like Mark Thompson, who value reliability and operational efficiency. Investing in high-quality graphite materials is only part of the equation; proper care is equally important.
10. Beyond Cleaning: Exploring Advanced Surface Treatments for Graphite Electrodes?
While meticulous cleaning maintains the inherent properties of a graphite electrode, sometimes applications demand enhanced performance characteristics. This has led to the development of various advanced surface treatments and modifications. These go beyond simply cleaning the surface and aim to alter its fundamental property profile for specific benefits. Let’s explore a few examples:
- Anti-Oxidation Coatings: Graphite tends to oxidize at high temperatures in the presence of air, leading to increased consumption, especially in EAFs or other high-temperature processes. Applying specialized coatings (e.g., based on silicon carbide, alumina, or other refractory materials) can create a protective barrier, significantly reducing oxidation loss and extending electrode life. These coatings need to be carefully selected to ensure they don’t negatively impact electrical conductivity or contaminate the melt.
- Surface Functionalization (Electrochemical): For electrochemical sensing and catalysis, the graphite electrode surface can be deliberately modified to enhance its performance. This might involve:
- Electrochemical deposition of metallic nanoparticles (like gold or platinum) to catalyze specific reactions.
- Covalent attachment of specific molecules or polymers to create selective binding sites for target analytes.
- Plasma treatment to introduce specific functional groups (like oxygen or nitrogen groups) that alter surface energy and interaction with the electrolyte or reactants.
These modifications aim to improve sensitivity, selectivity, or reaction rates for specific electrochemical measurements, pushing the boundaries beyond what a simple polished graphite electrode can achieve. We often see a trend towards more tailored electrode surfaces in advanced analytical chemistry.
- Impregnation: Certain graphite grades might be impregnated with materials like resins or pitch before final graphitization and baking to reduce porosity and improve strength or oxidation resistance. While typically part of the manufacturing process, post-treatments involving impregnation with specific materials (like copper for improved conductivity in some niche applications, or antimony for wear resistance) are also explored, though less common for standard graphite electrodes.
These advanced treatments represent specialized solutions tailored to specific challenges. While standard cleaning focuses on maintaining the baseline performance of products like UHP graphite electrodes or graphite blocks, surface modification offers a pathway to enhanced capabilities for demanding applications. This provides valuable insight into the ongoing innovation within the graphite industry. The selection and application of these treatments require significant expertise to ensure they deliver the desired benefits without introducing new problems.
Key Takeaways for Electrode Cleaning and Maintenance:
- Cleanliness is Critical: A clean graphite electrode surface is vital for optimal electrical conductivity, low consumption, consistent performance (in EAFs), and accurate electrochemical measurements (sharp peak, reliable signal).
- Know Your Contaminants: Identify likely sources of fouling (oil and water, dust, process residues) to choose the right cleaning method.
- Use Proper Tools: Employ soft brushes, lint-free cloths, appropriate solvents (IPA, acetone, DI water), and safety gear. Avoid harsh mechanical actions unless necessary and done carefully.
- Follow a Methodical Procedure: Inspect, dry clean (compressed air), wash (solvent wipe/rinse), dry thoroughly, and re-inspect. Protect threads.
- Consider Ultrasonic Sparingly: Useful for deep cleaning but use with caution to prevent damage. Control time and rinse well.
- Electrochemical Prep is Rigorous: Requires polishing (alumina/diamond), thorough rinsing, often ultrasonic cleaning, and sometimes electrochemical activation to achieve a reproducible surface. Monitor with CV peak analysis.
- Prevent Damage: Handle carefully, protect threads, use correct torque, avoid thermal shock, and check chemical compatibility. Breakage prevention is key.
- Verify Cleanliness: Use visual inspection, wipe tests, and for electrochemical work, CV testing.
- Store and Handle Properly: Keep electrodes clean, dry, protected (especially threads), and handle with clean equipment/gloves to minimize re-contamination.
- Advanced Treatments Exist: Coatings and functionalization can enhance properties like oxidation resistance or electrochemical activity for specific needs.
By implementing these guidelines, users of graphite electrodes can ensure they get the best performance and lifespan from these critical components, minimizing operational issues and maximizing efficiency.
Post time: 04-21-2025